Interview The Kanto team
Images TDRI and NakNak (Yenwen Tseng)
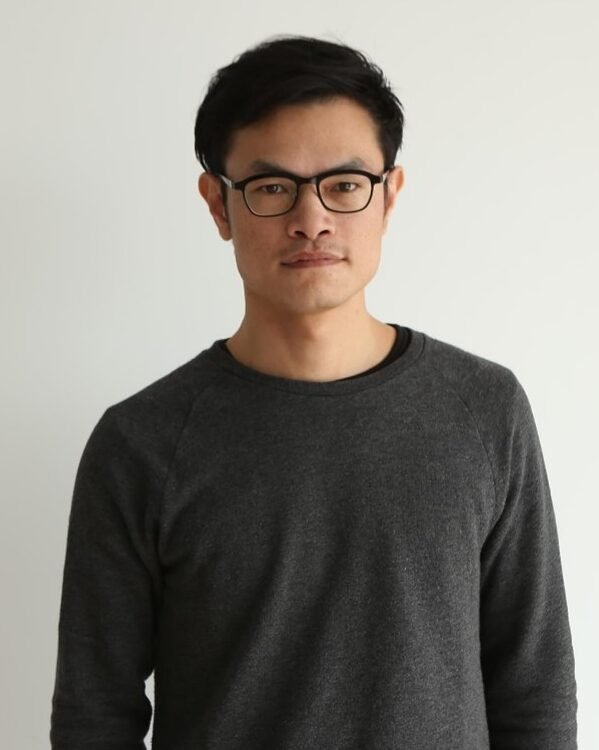
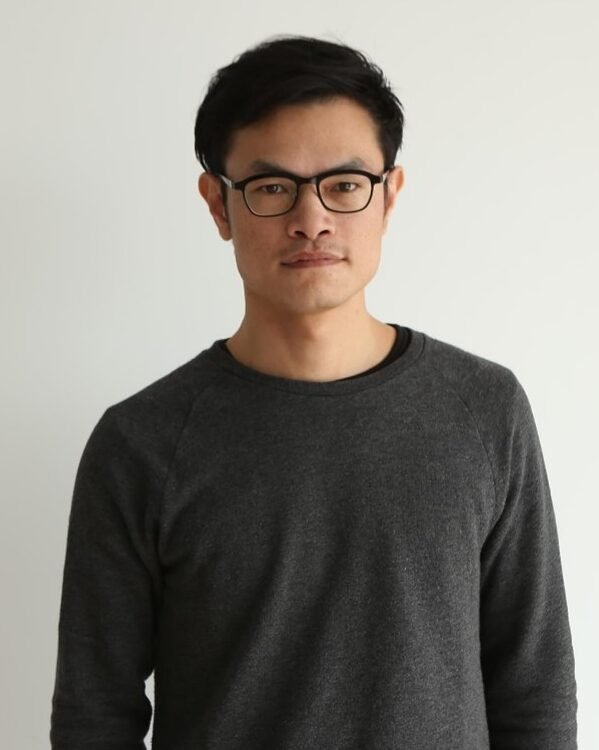
Hi Yenwen, welcome to Kanto! As the founder of your eponymous circular design studio, home décor and public objects brand NAKNAK Design, and an industrial designer with experience in Stockholm, New York, and Taiwan, your award-winning work bridges global design thinking with local manufacturing expertise. Can you share how these different environments shaped your design philosophy?
Yenwen Tseng, design director, NAKNAK Design: Hello, and thank you, Kanto! In Stockholm, I focused on learning the design process: observing and identifying problems, generating concepts, and refining outcomes to communicate ideas effectively. I paid particular attention to the phase after concept formation, which often takes two to three times longer to explore the best expression of the idea.
In New York, I gained a deep understanding of how design studios operate. This included project initiation, background analysis, interpreting requirements, coordinating resources, conducting presentations, and delivering outcomes. As a designer in the studio, I had to grasp each project’s core while also expressing my insights.
In Taiwan, I developed practical manufacturing knowledge: communicating with factories, controlling costs, and assessing production feasibility. I also learned how to integrate Taiwan’s manufacturing capabilities to enhance the traditional OEM industry, elevating product value and bringing greater design appeal to locally made products.
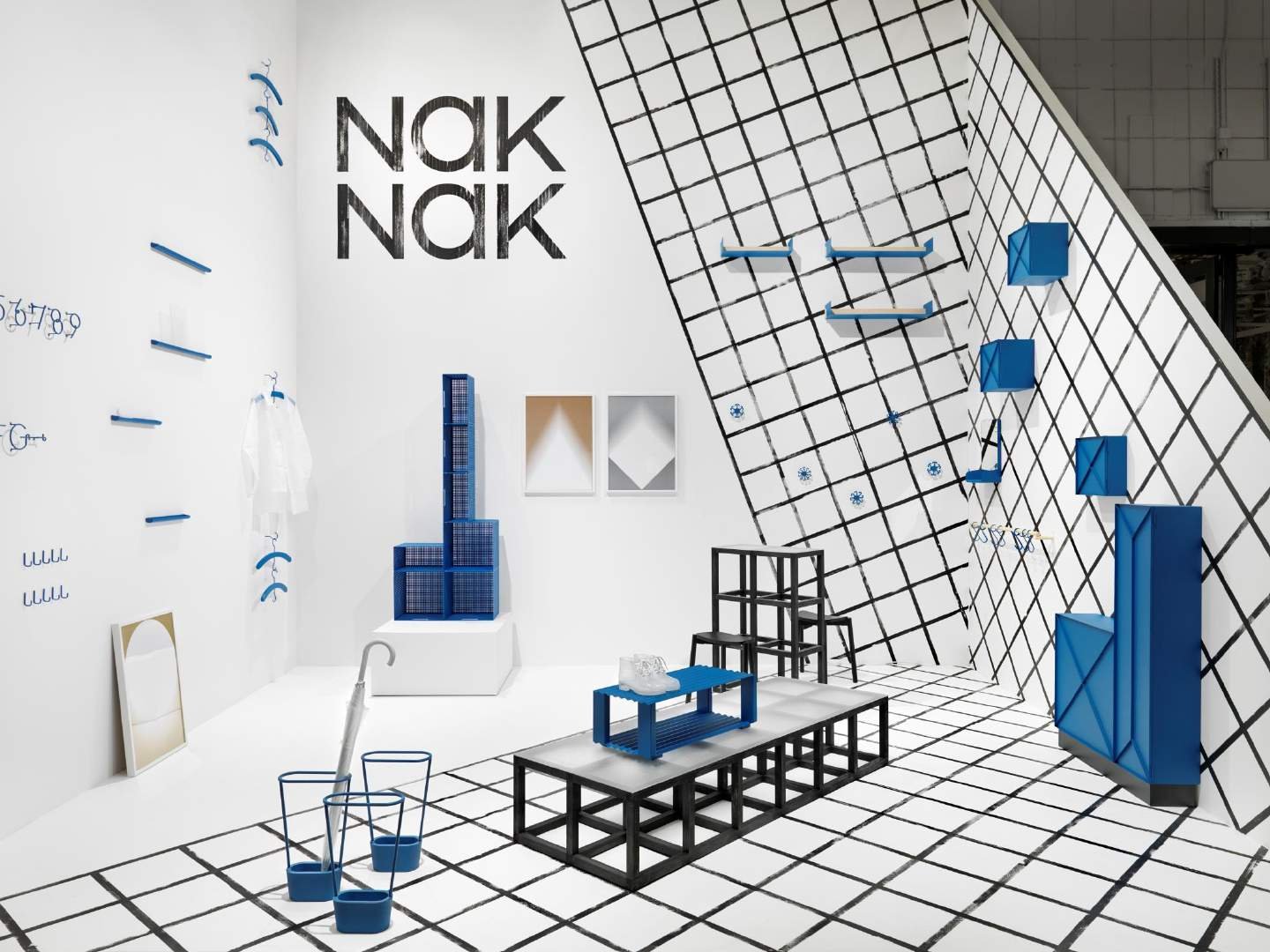
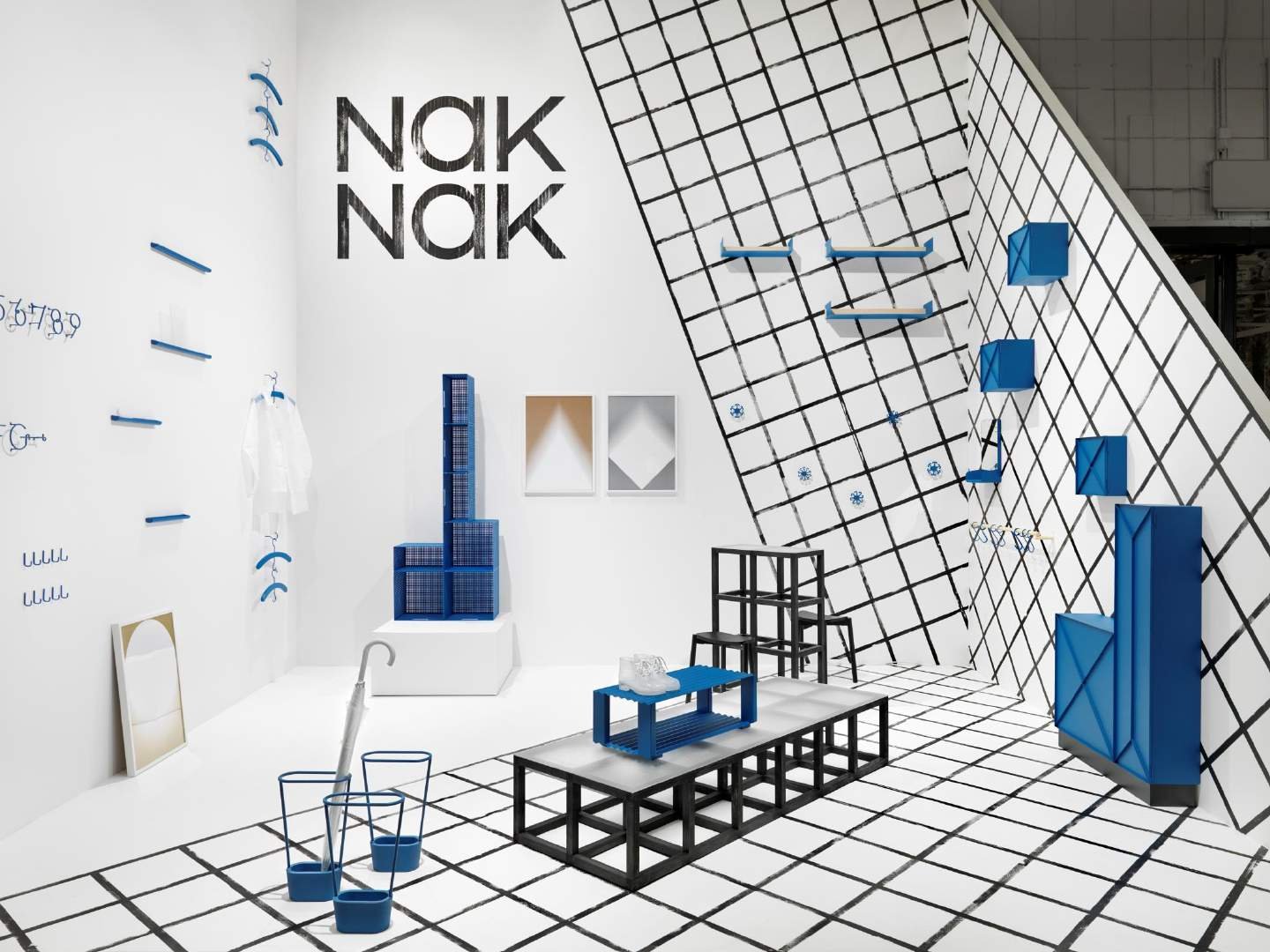
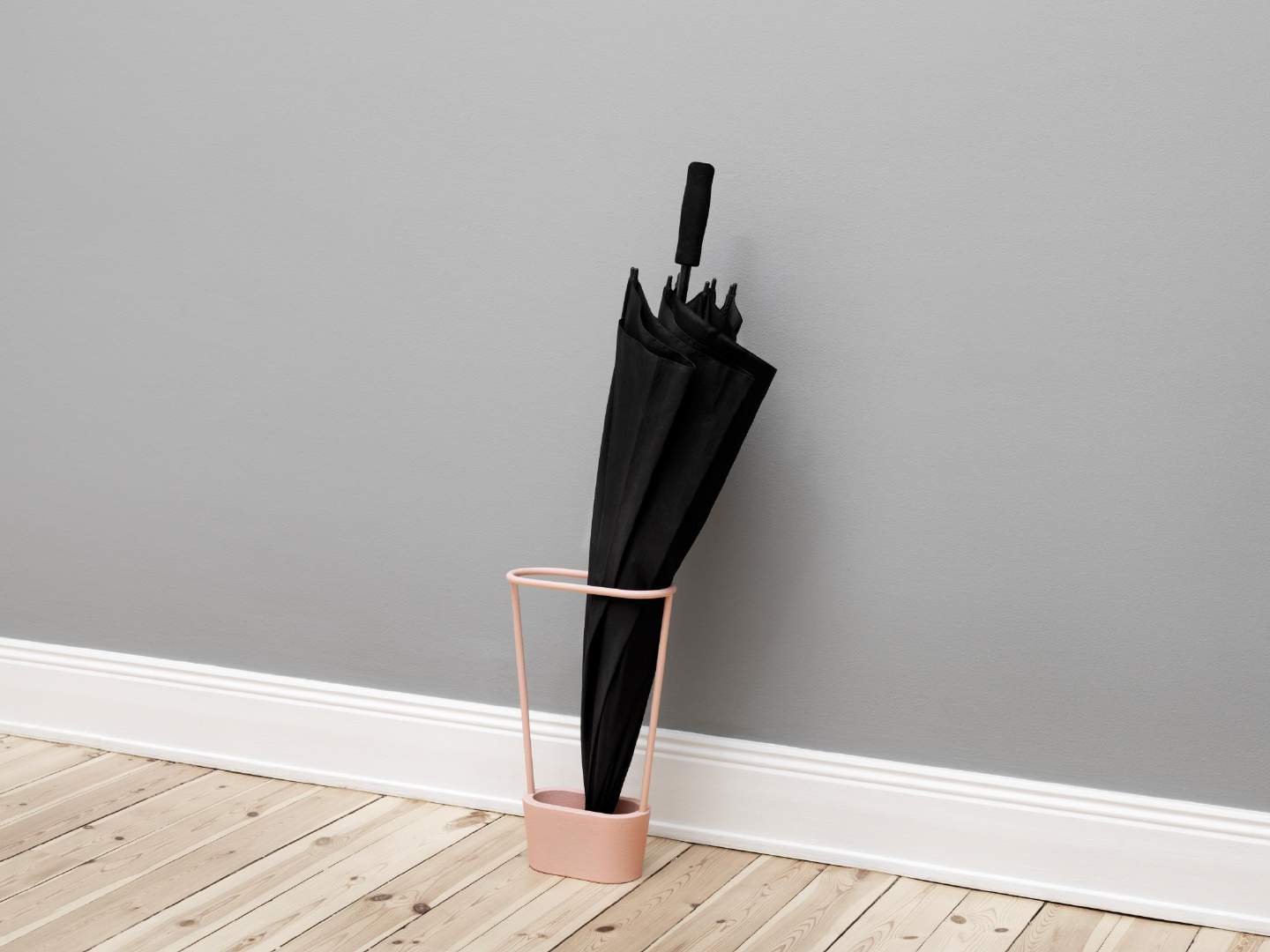


Your brand NAKNAK has gained a lot of acclaim, starting as a home goods brand before broadening reach to public-facing objects, all anchored on the principles of circular design. Can you share a specific project within the brand where circular design principles directly influenced the outcome? What were the challenges and successes?
Yenwen Tseng: I established NAKNAK in 2015 to integrate Taiwan’s local manufacturing resources with international design collaborations, creating simple, functional objects. Since 2018, the focus has shifted toward often-overlooked public space facilities, such as trash bins, umbrella stands, fire extinguisher accessories, and house numbers.
The Magong Ferry Terminal, or Penghu South Sea Transportation and Tourism Waiting Room, is a strong example of circular design in action. The original goal was simply to design a visually appealing bench, but given the project’s location on an island facing marine waste challenges—and Taiwan’s Maritime Port Bureau efforts to reshape the local marine brand—it became an opportunity to introduce circular materials.
There were challenges, including budget constraints, the complexity of working with marine waste materials, and a tight timeline. However, the properties of these materials made the bench well-suited to the port’s climate. It is weather-resistant, easy to clean, and when damaged, the marine waste panels can be recycled back into the factory as raw material for new panels, creating a true circular system.
Beyond functionality, the project sparked conversations about circular materials, establishing a strong identity for the ferry terminal. It also paved the way for our next seating project at the Penghu Visitor Center.
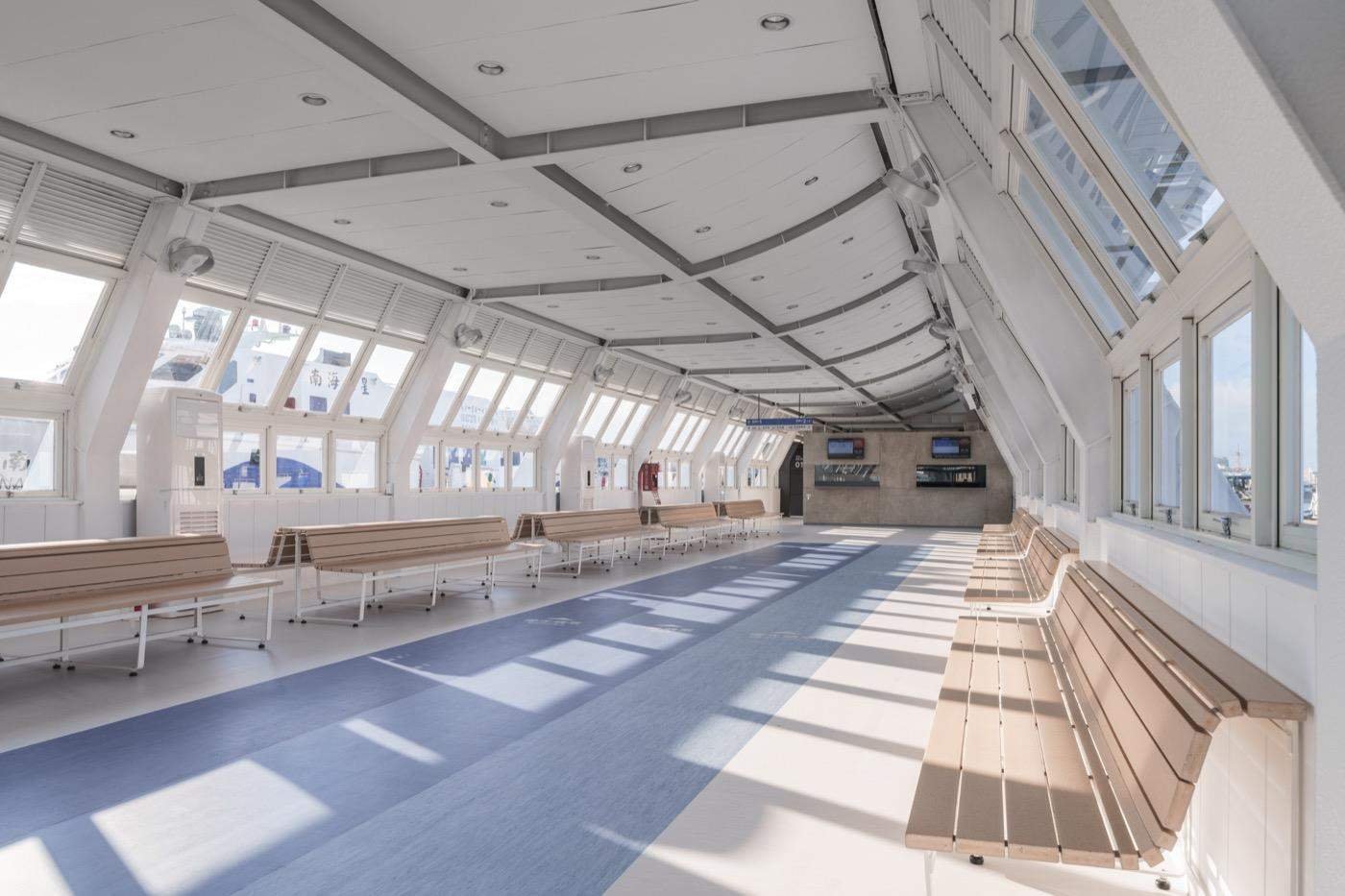
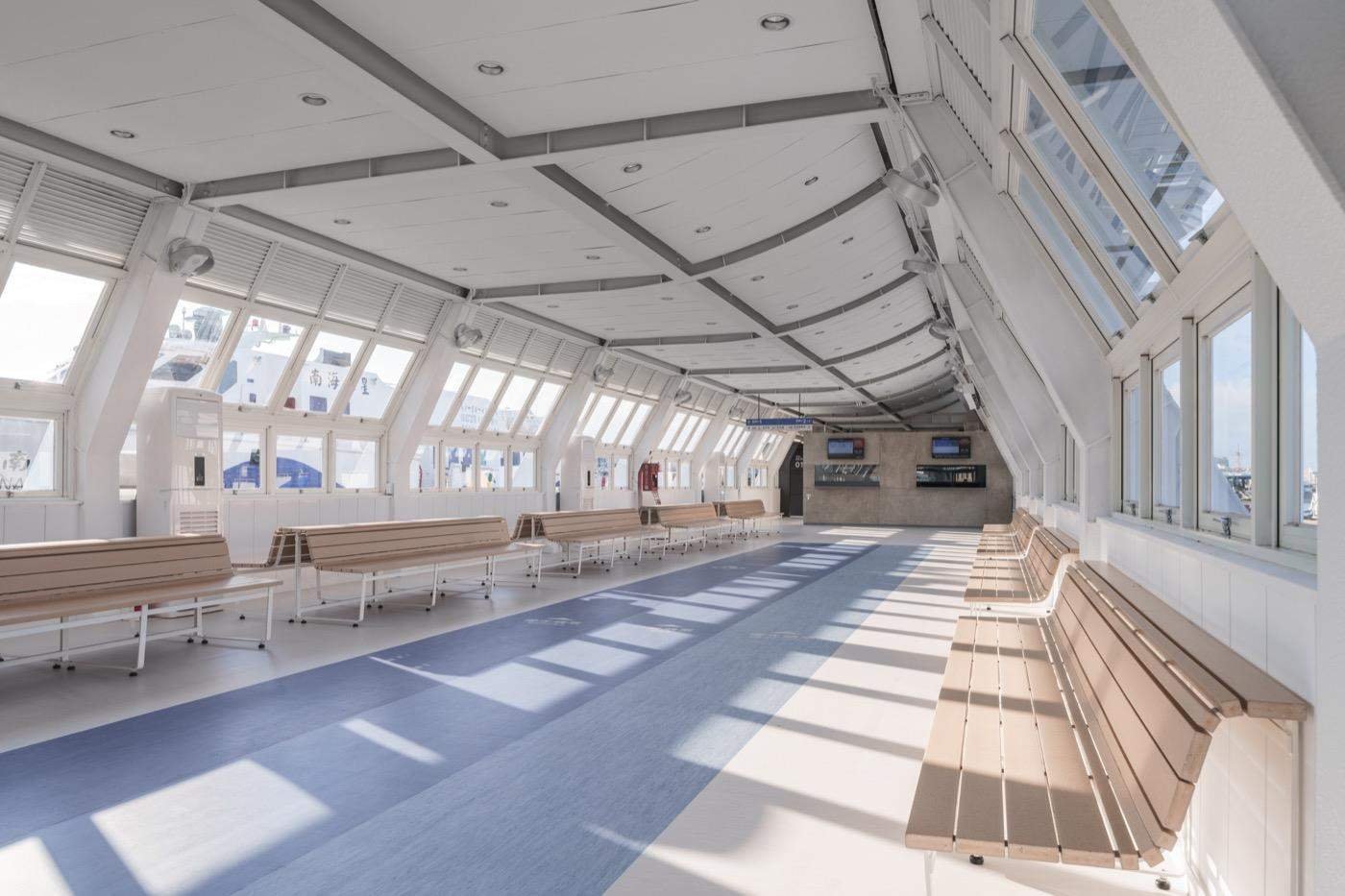
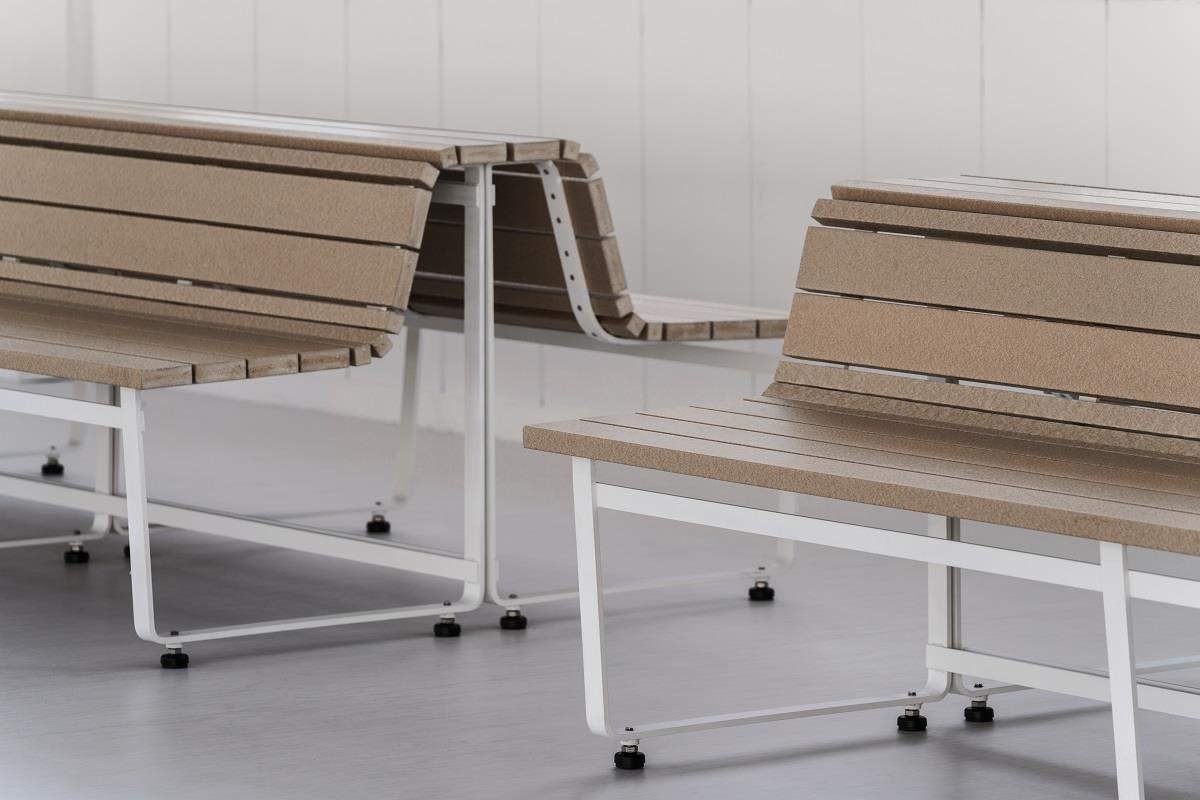
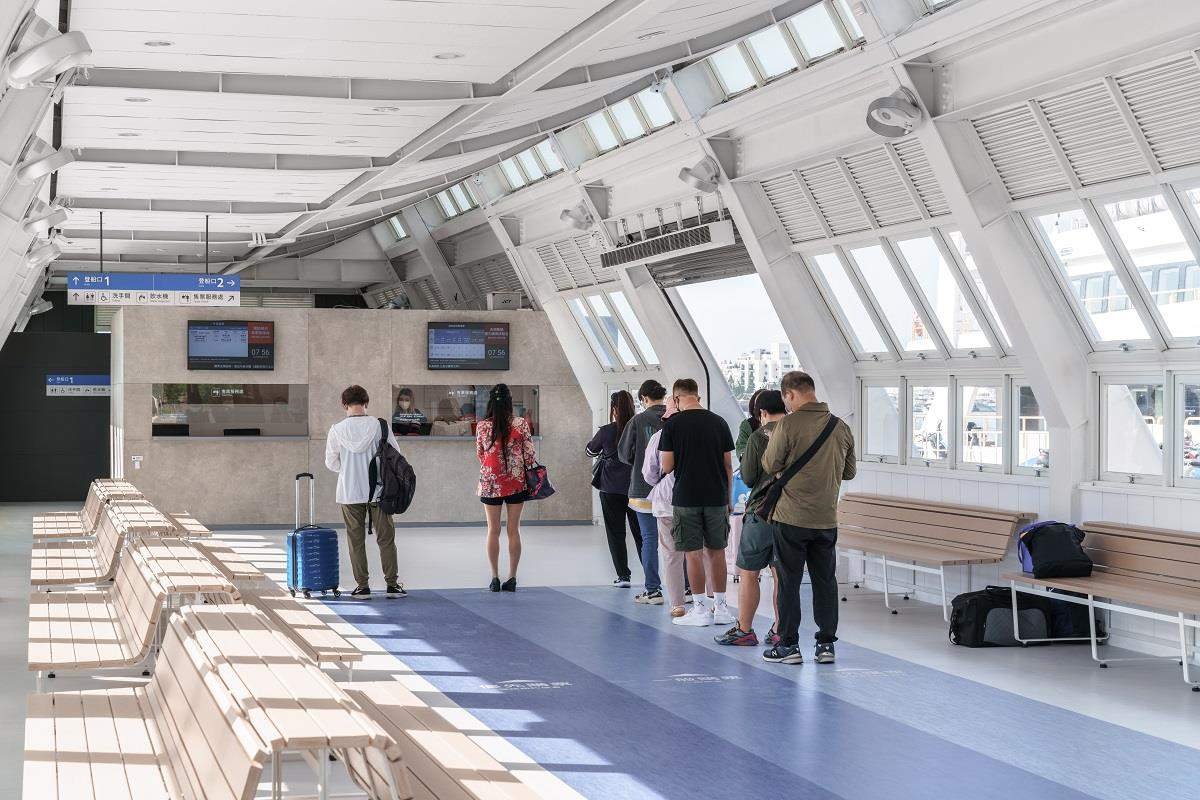
Penghu South Sea Waiting Room: Public Seating from Marine Waste
The Penghu South Sea Waiting Room is an essential facility for passenger transfers to Qimei and Wang’an completed in 2009. The Maritime and Port Bureau, in partnership with the Taiwan Design Research Institute (TDRI), initiated a renovation project to rejuvenate its largely unchanged interiors. NAKNAK designed new public seating using recycled marine waste, incorporating over 70,000 PET bottles, oyster shell powder, and styrofoam. The seats are ergonomic, movable, and offers storage space underneath for travelers.
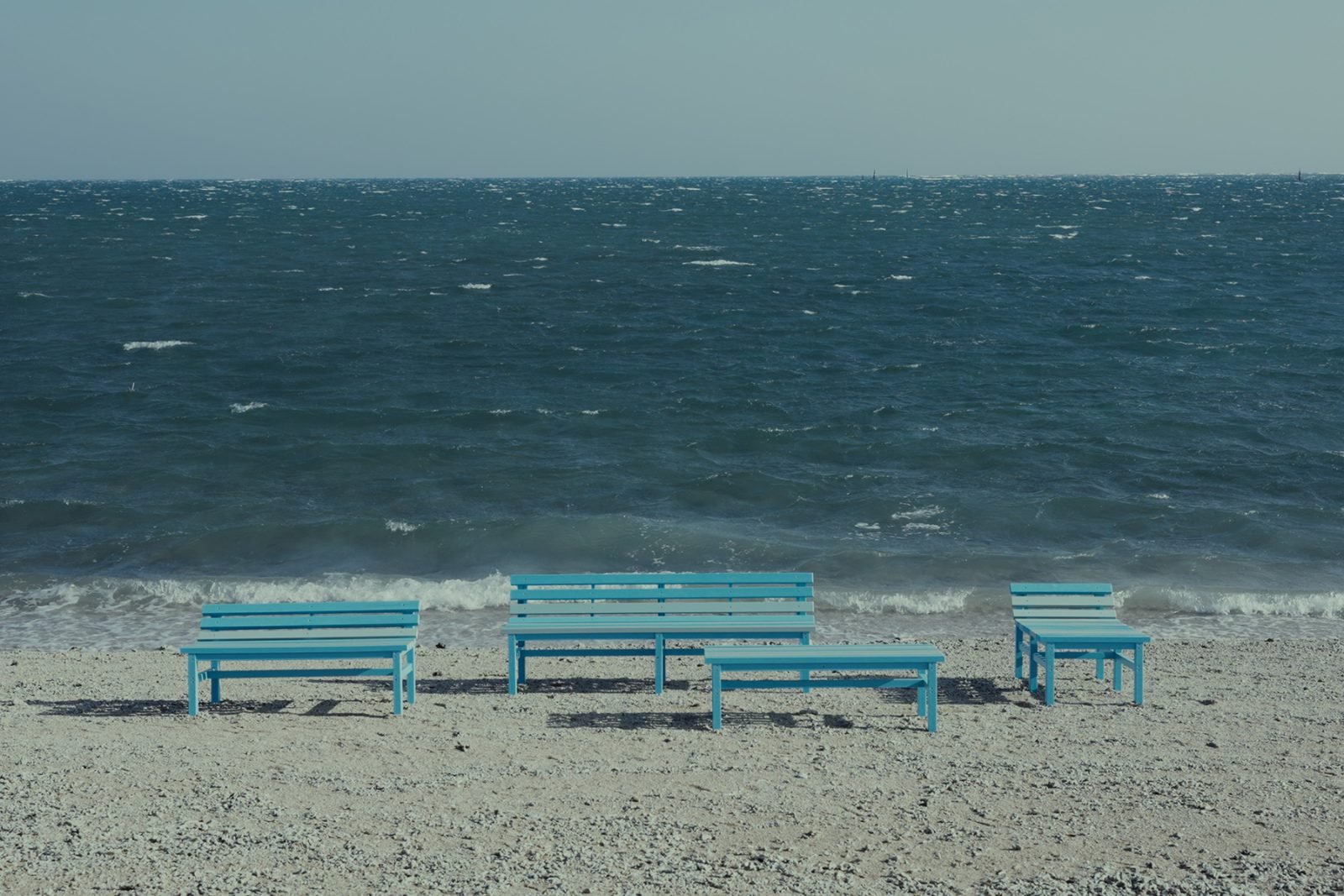
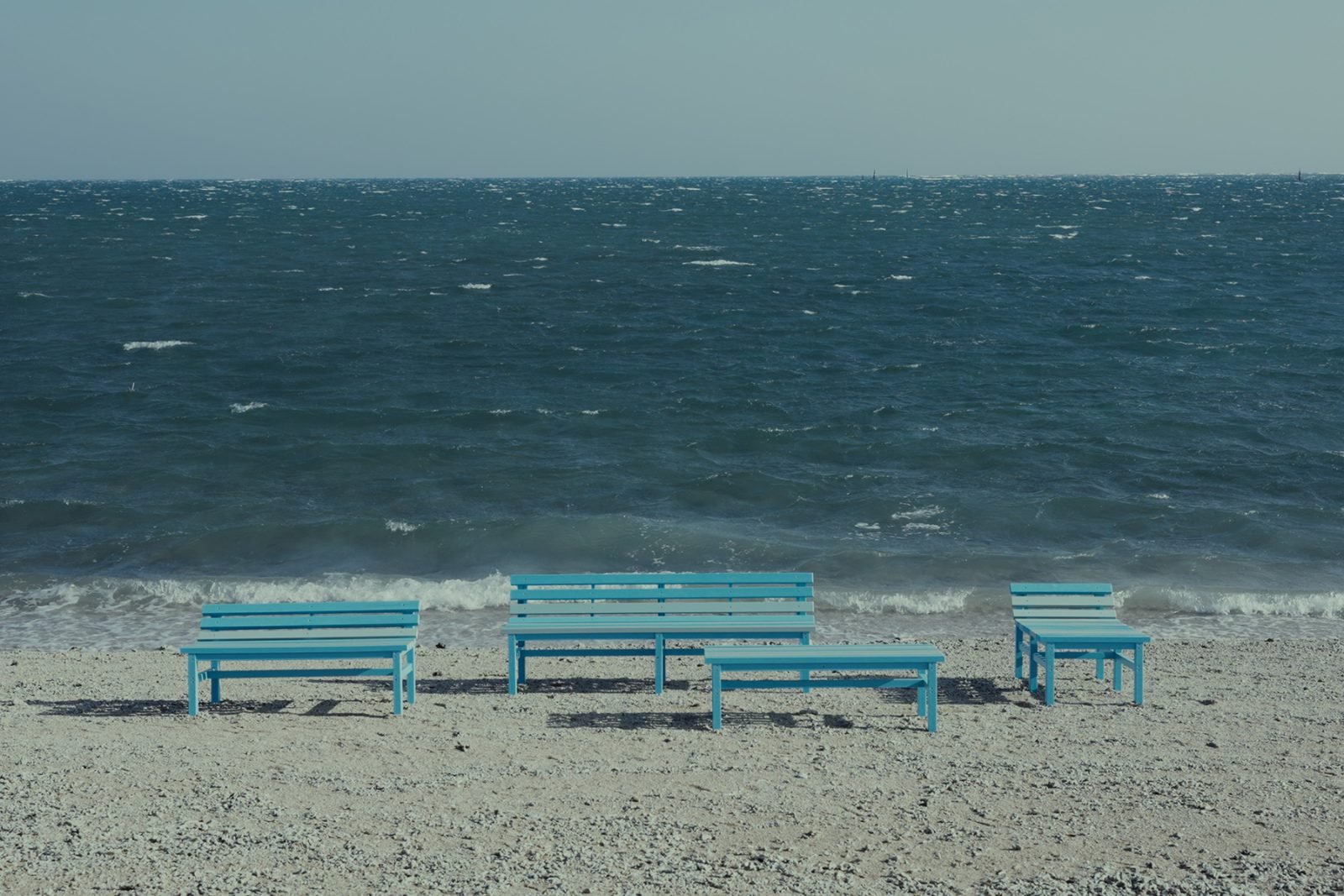
New Life Cycle of Penghu Marine Waste: Marine Waste Public Seating
The Penghu Marine Waste Reuse Project, led by the Penghu Management Office, aimed to integrate recycled marine debris into the public realm. NAKNAK introduced seats made from local marine waste at visitor centers across the island. Discarded styrofoam pieces from beach cleanups were processed into seats for the Houliou and Qitou Visitor Centers, giving residents and visitors a glimpse of the possibilities marine waste reuse can offer.
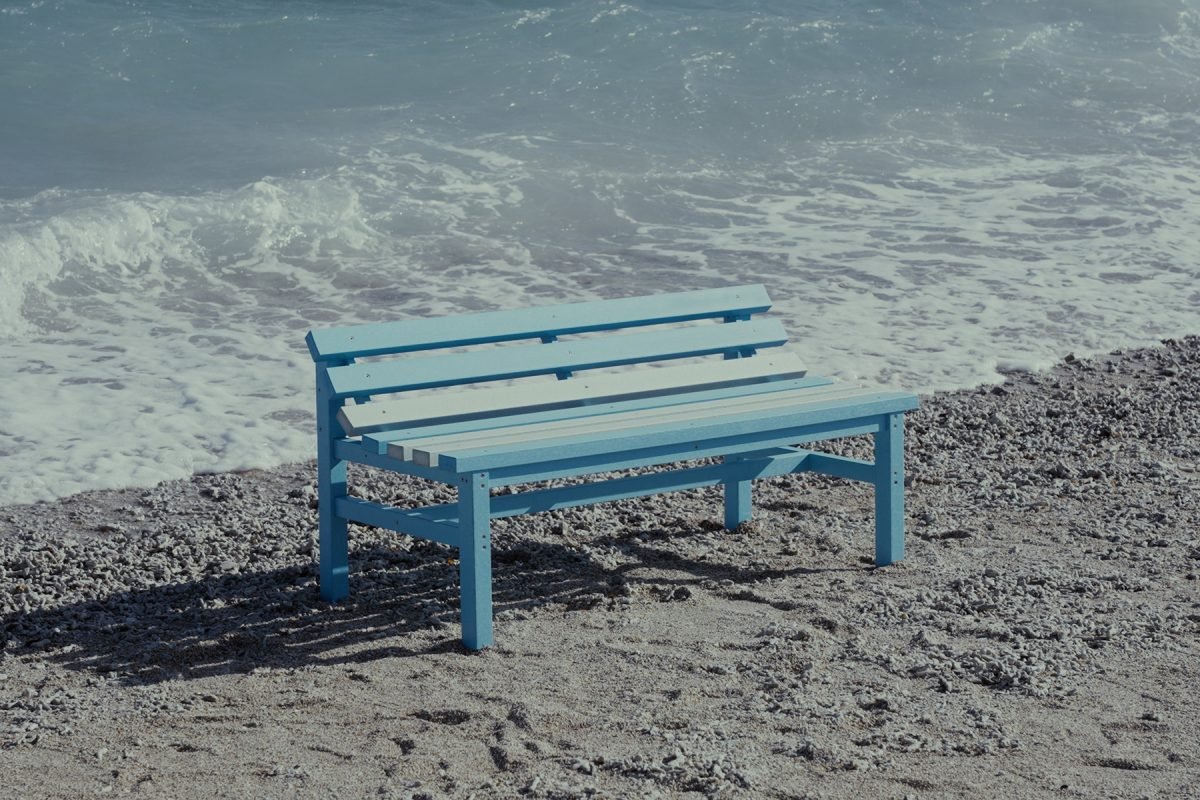
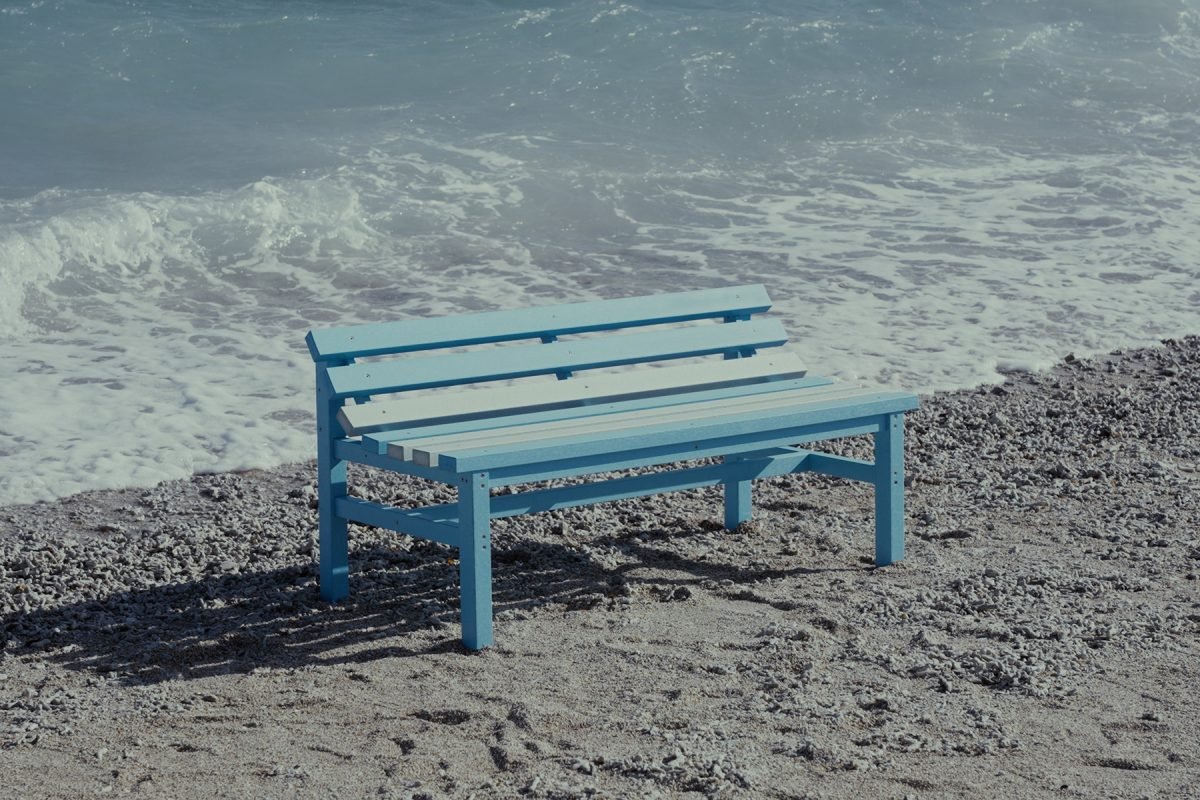
Sustainability is a major concern in design today and while it is easy to say that it should be a standard, complexities exist. You’ve made sustainability an inalienable part of NAKNAK’s genius through circularity. How do you ensure it is a fundamental practice in your work rather than just a concept?
Yenwen Tseng: Sustainability in design must be approached with feasibility in mind. Circular design concepts need to be applied where they make sense within a project’s scope.
For a company of NAKNAK’s scale, integrating circular principles into every product may not align with commercial demands. I see two effective approaches: large corporations applying these concepts selectively, such as Acer and Asus incorporating circular materials in some products, or executing circular projects independently, like our Magong Ferry Terminal bench. The key is to introduce circularity at the right time and in the right context.
Indeed. Many designers aim for innovation, but practicality can be overlooked. You’ve been at this for a while. How do you balance creativity with functionality?
Yenwen Tseng: Innovation is most effective when grounded in practicality. This makes the design feel more logical and ensures feasibility in production. Taiwan’s manufacturing resources are particularly valuable in this regard, allowing creative concepts to be realized at scale. Integrating creativity, functionality, and production considerations makes the design process far more engaging.


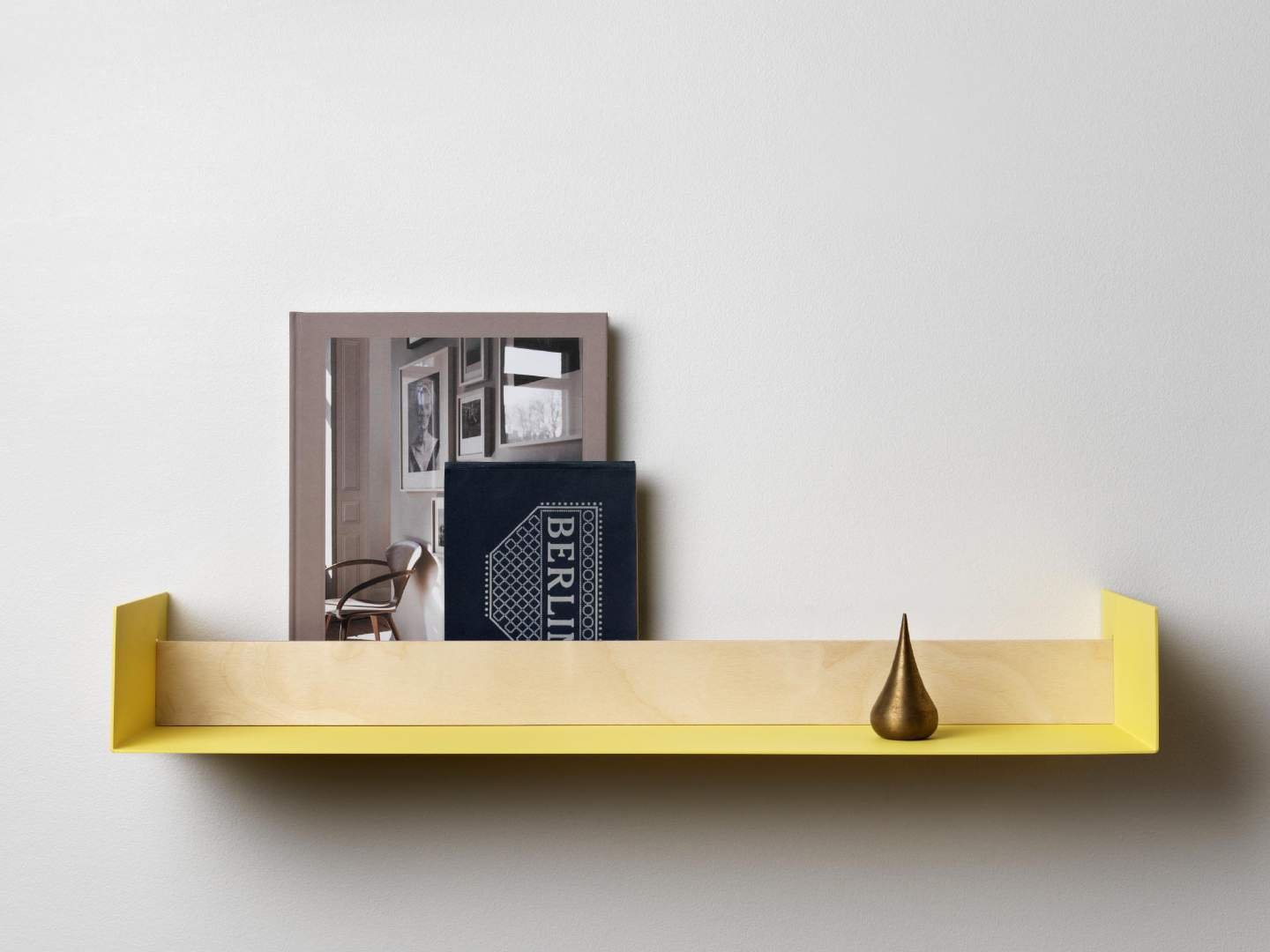
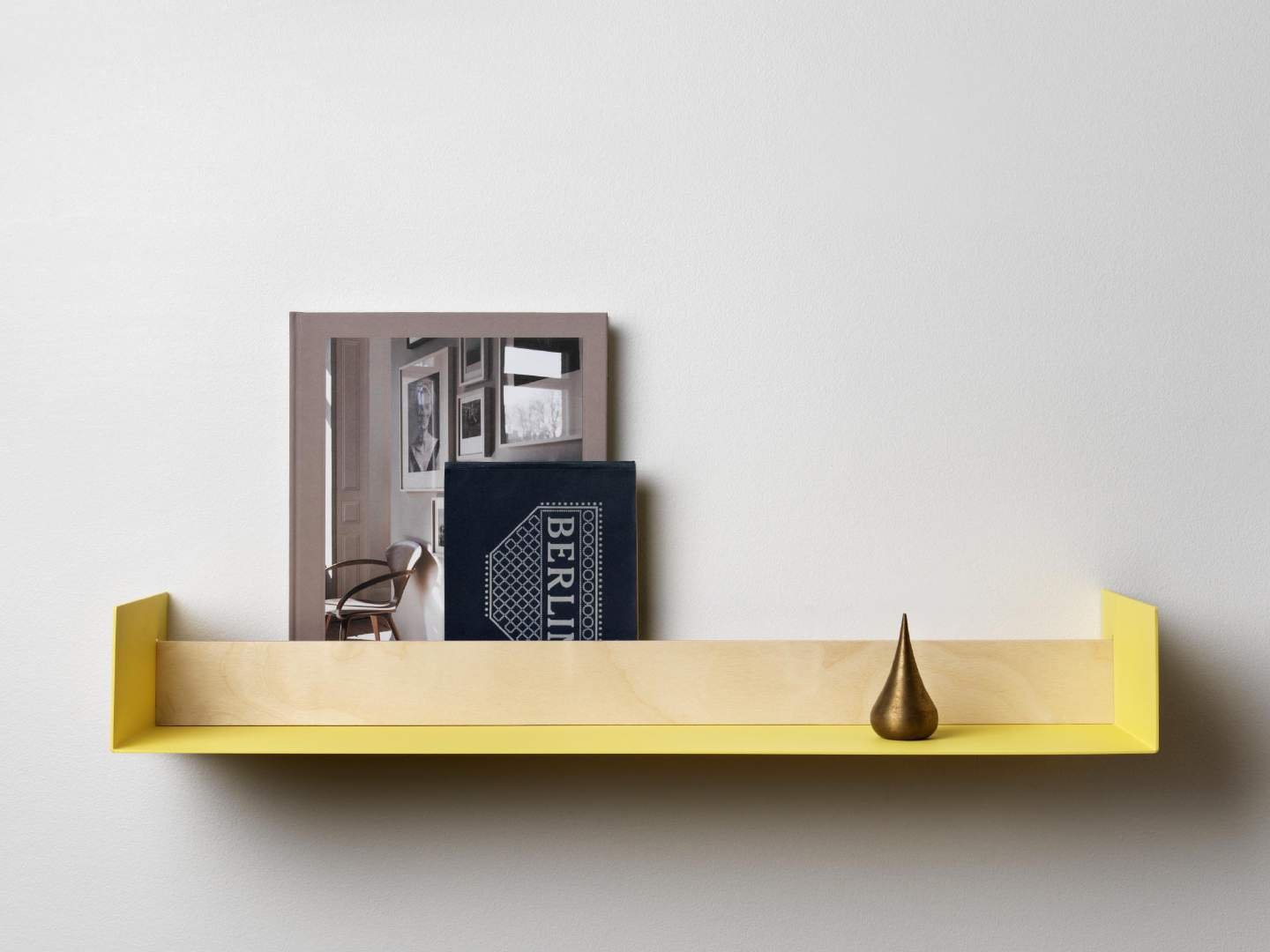
Let me angle my lens closer to home. How do you see sustainability evolving in design, especially in Southeast Asia?
Yenwen Tseng: Southeast Asia generates a significant amount of waste. The Philippines, for example, struggles with marine debris management. Because of this, people in the region regularly encounter waste in their surroundings.
At the same time, the region has strong labor-intensive industries and R&D capabilities, making it well-positioned to repurpose waste into raw materials. This creates an opportunity for Southeast Asia to take the lead in developing and applying circular materials.
Traditional craftsmanship is often seen as being at odds with modern sustainable practices. How do you navigate this tension in your work?
Yenwen Tseng: Traditional craftsmanship and circular practices can complement each other. Many circular materials, especially in early testing phases, rely on traditional techniques for prototype development.
New materials can also be shaped using traditional methods to highlight their unique characteristics. For example, waste fibers can be woven directly into products to emphasize their origins, or recycled fibers from factories can be repurposed into entirely new materials. Both approaches serve different stages of the circular process.
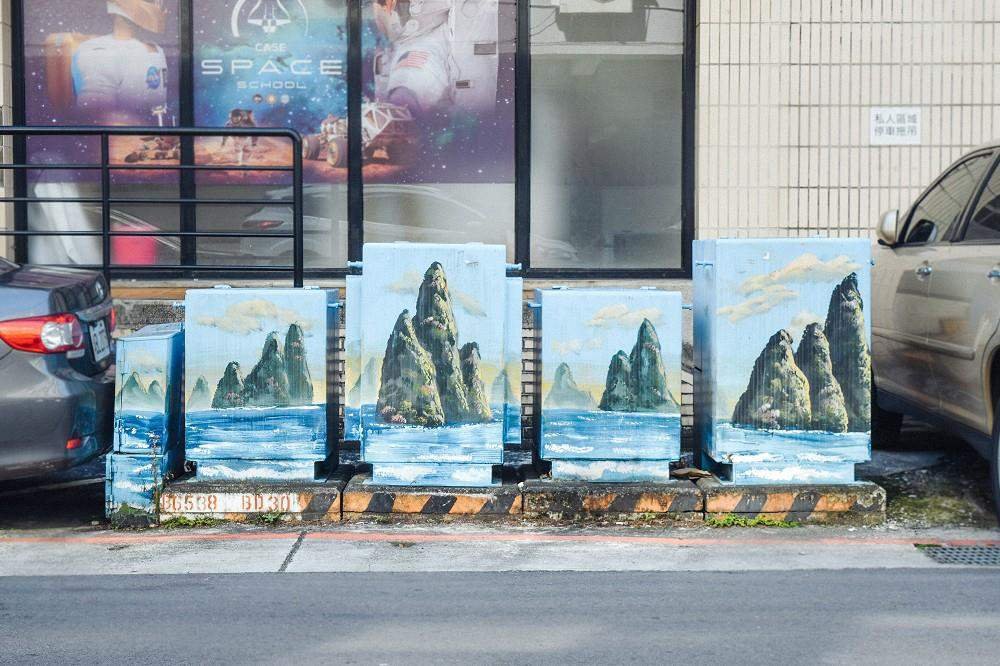
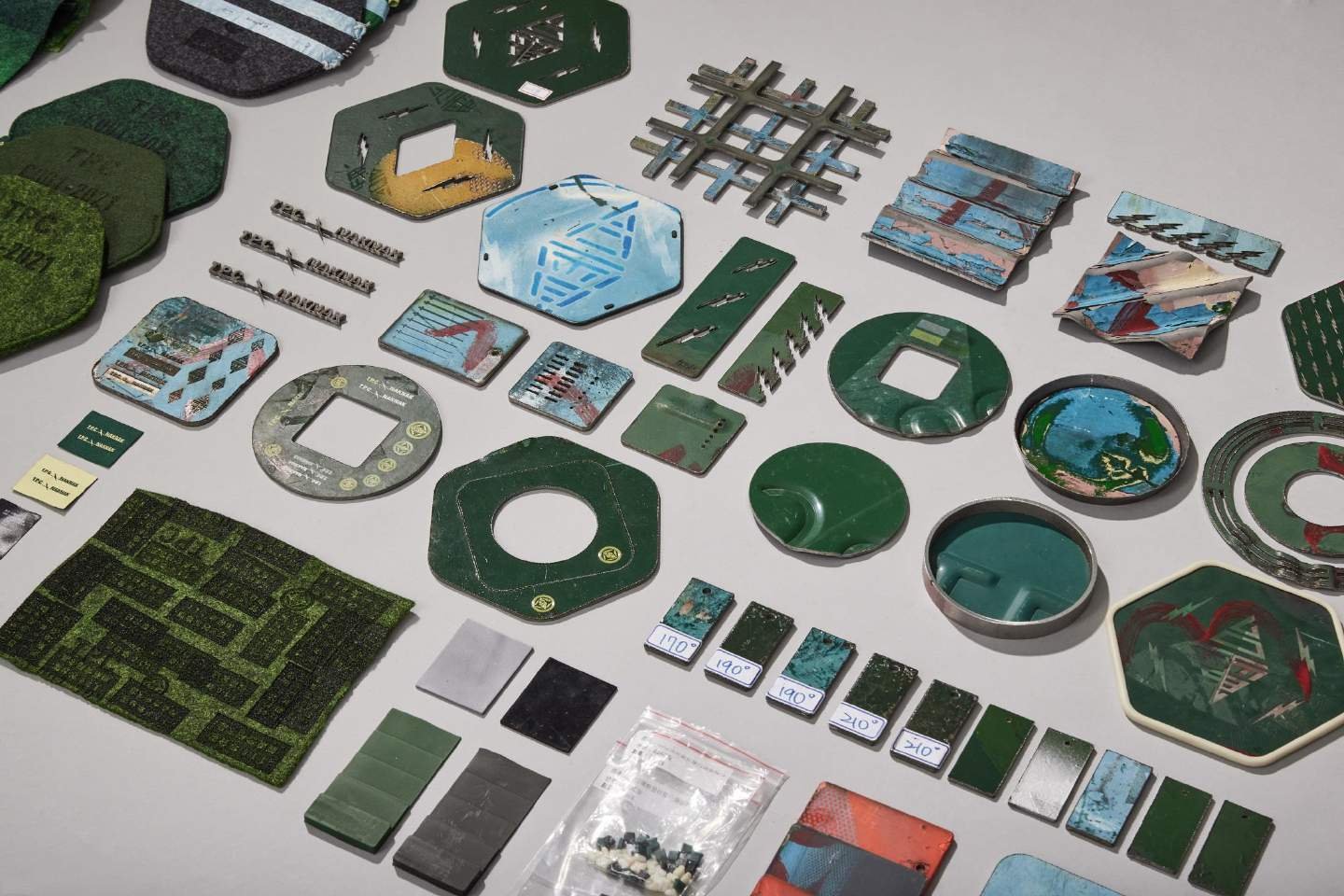

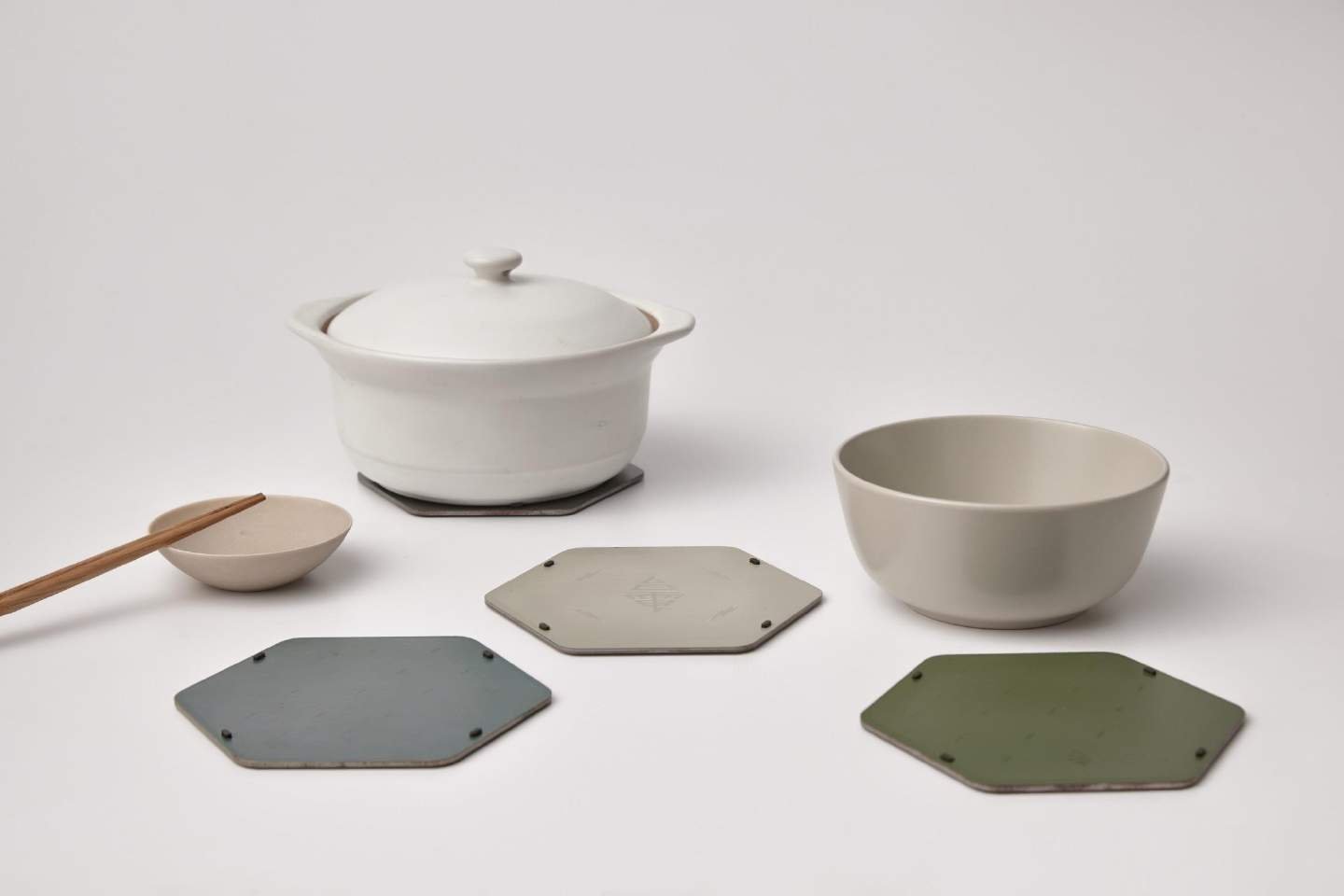
NAKNAK × Taiwan Power Company – Repurposing Project
In collaboration with the Taipower Cultural and Creative team, NAKNAK repurposed retired transformer boxes into multi-functional heat pads for home and gifting use. After extensive material experimentation, these heat pads featured the unique textures of the original boxes, complete with scratches and graffiti. Each pad retained its original texture and included a source code indicating its origin.
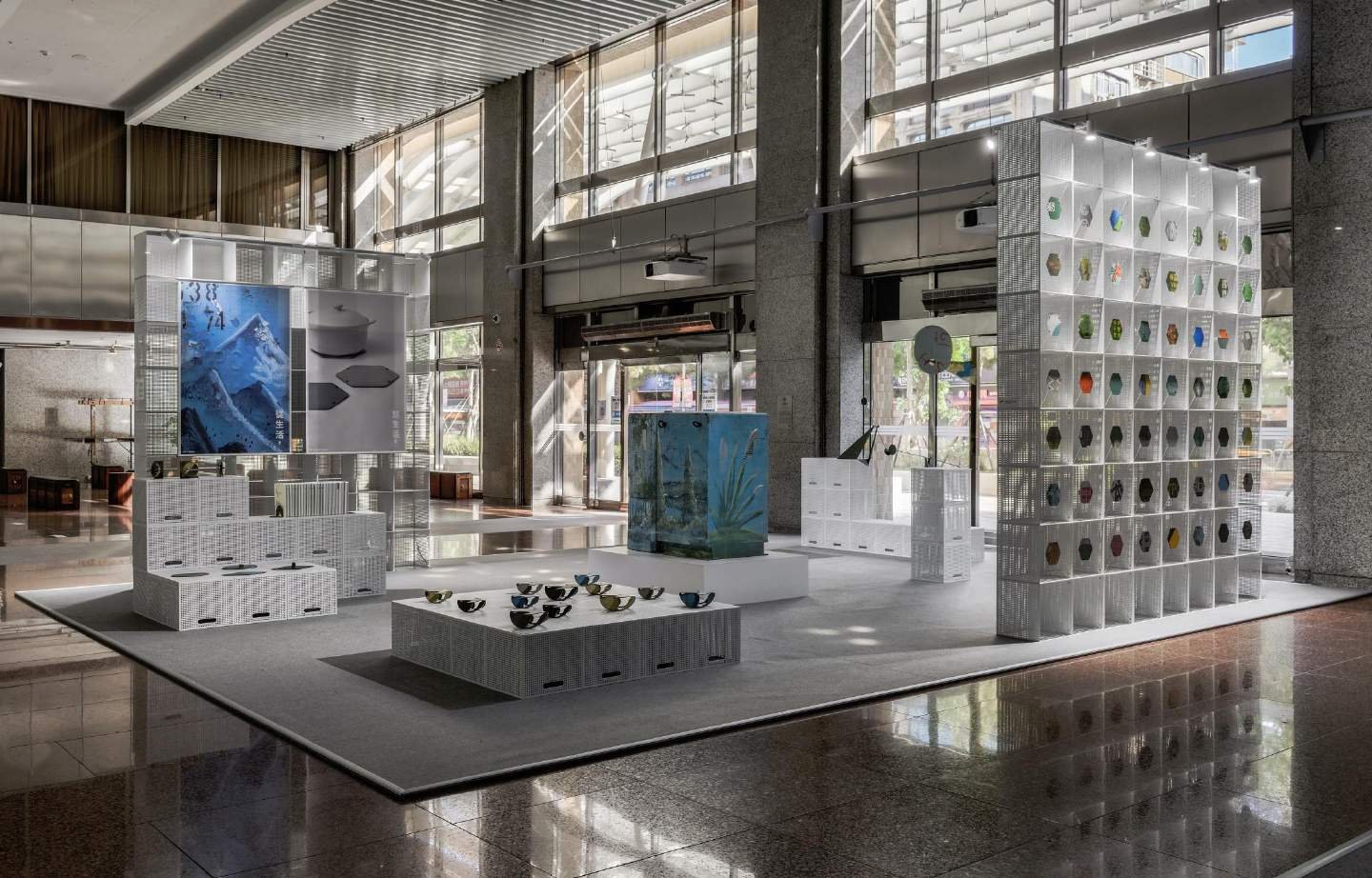
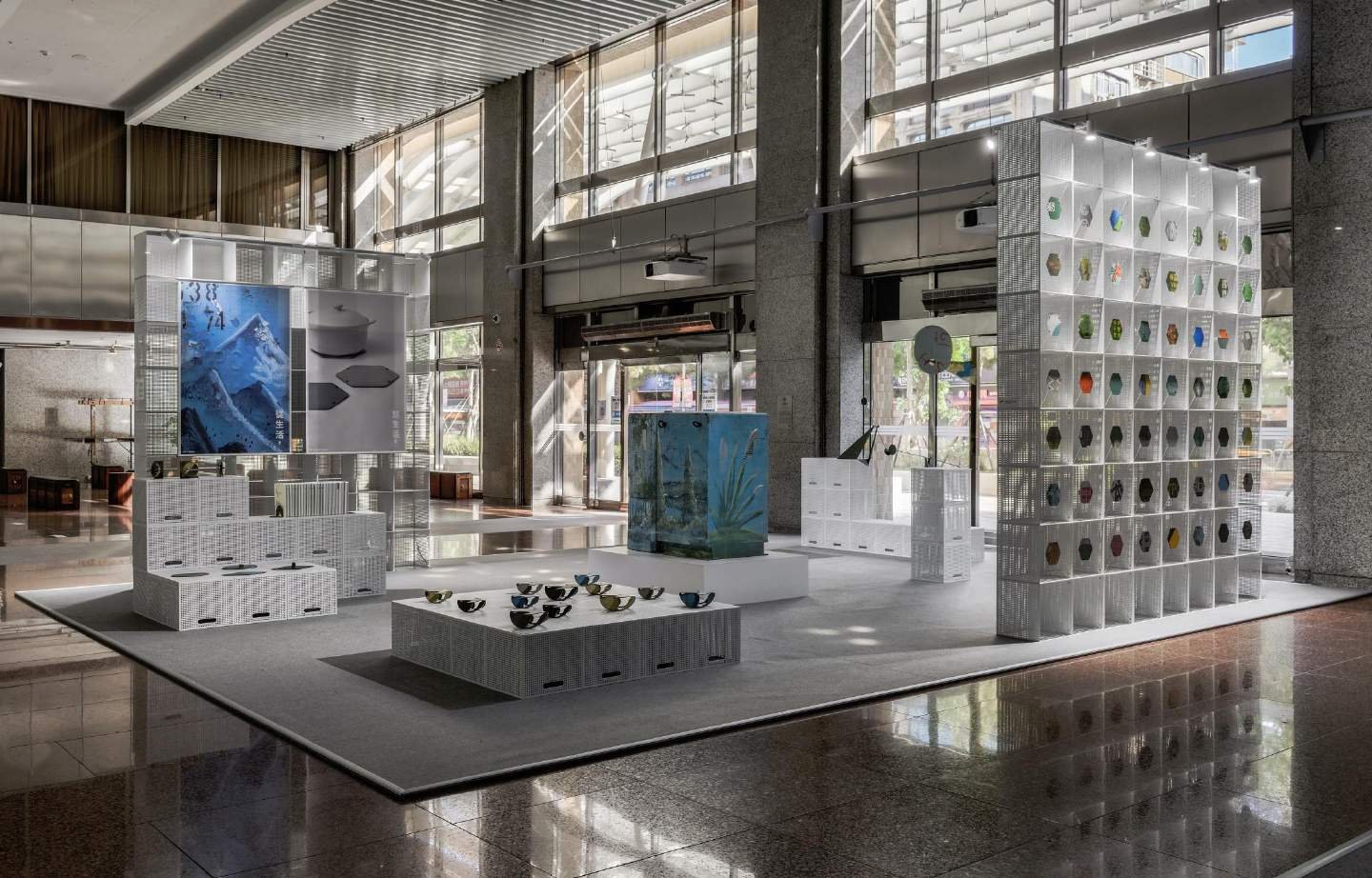
How have your experiences in different cultural contexts influenced your design philosophy? How can Filipino designers benefit from similar cross-cultural exposure?
Yenwen Tseng: In Sweden, design training centered on the essence of life and a more conceptual, philosophical approach. In New York, it was about commercial viability and business strategy. In Taiwan, it was focused on manufacturing, leveraging local resources to create practical, production-ready designs.
Each culture shapes design in distinct ways. In the Philippines, craftsmanship is a significant strength. The challenge is to merge handmade techniques with scalable mass production to create unique, locally produced designs.
Taiwan Design Research Institute has recently wrapped up an edition of Taiwan Design Week anchored on explorations in AI (artificial intelligence) use. What ethical considerations should designers like yourself keep in mind when integrating AI and advanced manufacturing into their work?
Yenwen Tseng: AI and advanced technologies should serve as tools rather than dictate design direction. A designer’s core values and original intent must remain clear. These technologies can assist in exploring possibilities and refining quality, but the essence of a design should remain in the designer’s hands.
There really is no sugarcoating the urgency and gravity of the global environmental crises we now face. What role or roles should designers play now in advancing sustainable means of creation such as circular design?
Yenwen Tseng: Designers should actively explore circular applications in every project. Understanding a project’s context and introducing circular materials at the right stage is crucial. The responsibility of driving circular design forward falls on designers, who must continually find ways to integrate these principles into their work. •


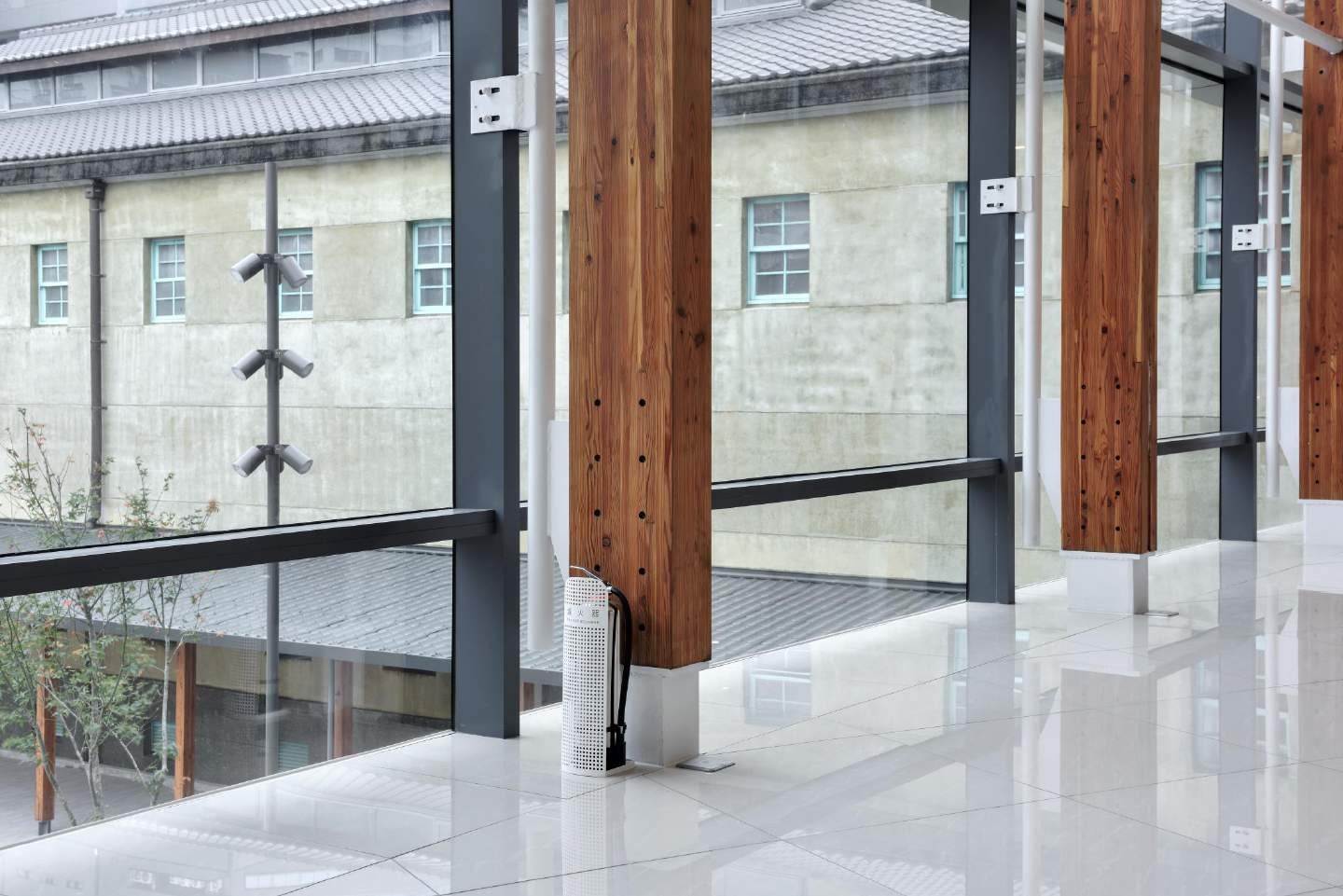
This interview was made possible by the Taiwan Design Research Institute (TDRI)