Interview Patrick Kasingsing
Images Foresso
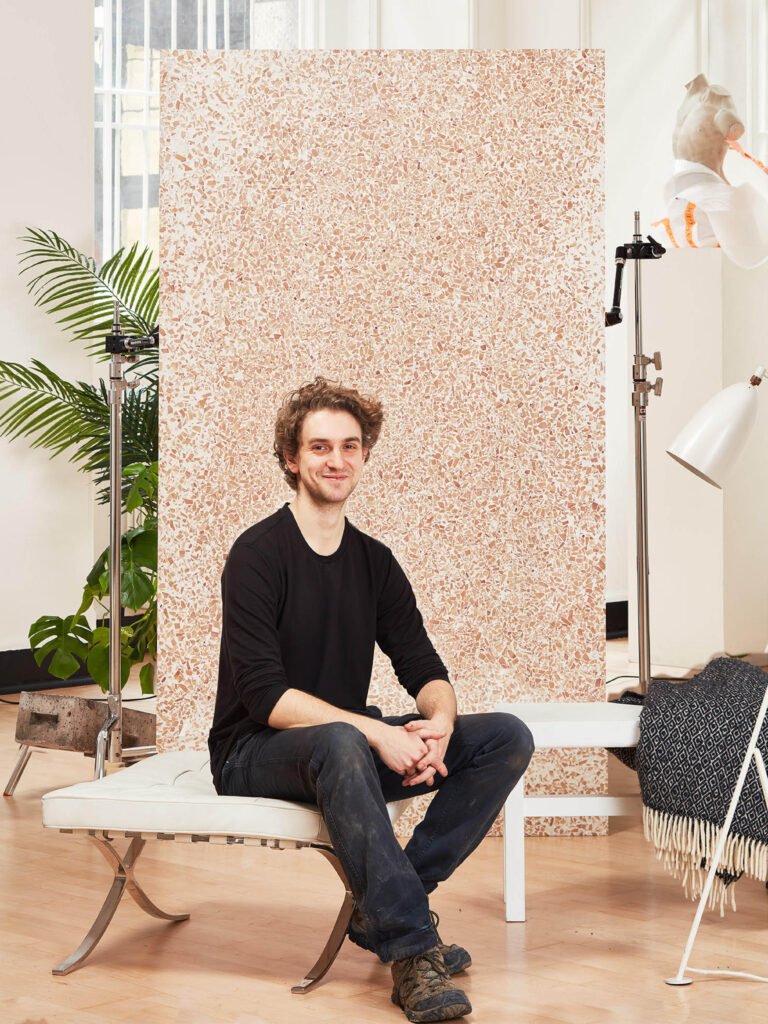
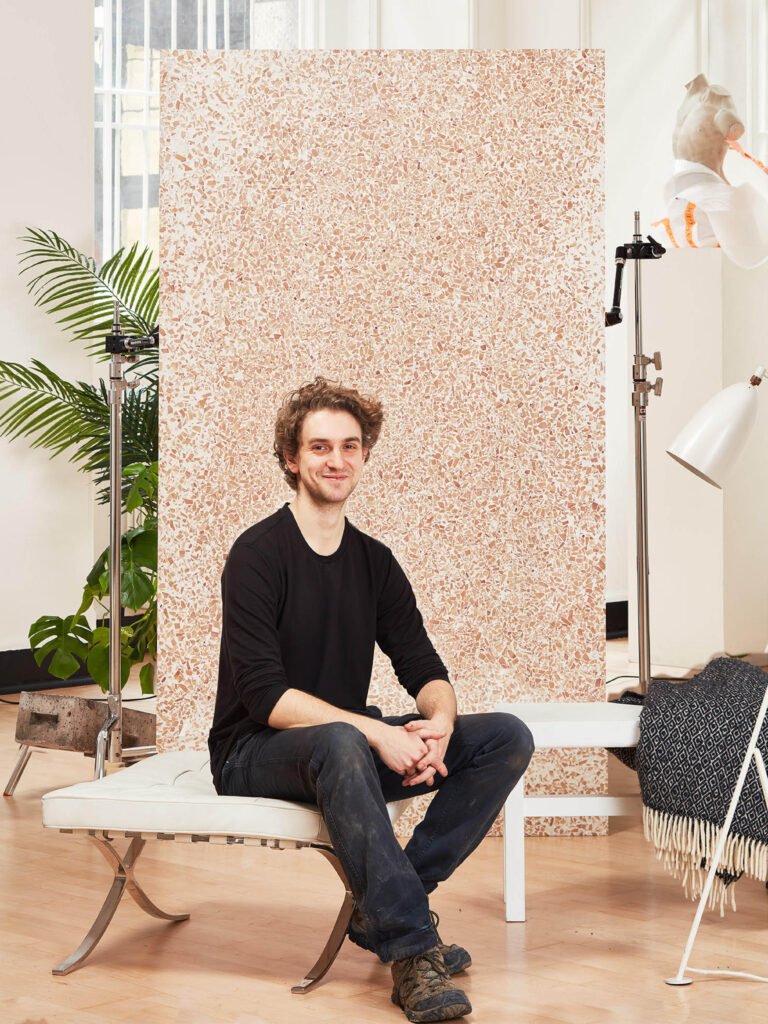
Hello! Kindly introduce yourself.
My name is Conor Taylor. Over the past few years, I have developed Foresso (the timber terrazzo) that we now manufacture in the UK using recycled materials.
What pulled you in into the world of industrial design?
I actually have a background in fine arts but as I was working in varied workshops, I started to fall in love with manufacturing. To me, it’s like a puzzle waiting to be figured out. I’m also a bit of a perfectionist, so it was great to be designing the process for a material that is so random in its aesthetic. I could relax and focus on how to better make it. Foresso has exploded in demand, and it’s a natural step to scale up into a much larger set-up for it. And I wanted to be part of a company that could follow a policy of ethics and constant improvement.
What spurred the development of Foresso? Was there a singular eureka moment that made you realize the potential of a product made from recycled waste materials?
I had been working for a carpenter on a variety of high-end projects. These kind of projects often have a very disposable culture about them, where the expectation is that it will all be torn out and replaced in a year or two. While I was processing all this beautiful British hardwood and high-end veneers, I got to thinking that there must be a use for the offcuts and planing waste rather than just disposing of it all.
It then struck me that I hadn’t seen a timber terrazzo before, and so I started experimenting. Right from the start I had some goals in mind. I wanted to use only offcuts and waste; it needed to be practical and great looking, and my ethical stance needed to be taken through the entire process, and now through our business. For me sustainability is not just about recycling; it’s also about knowledge of your materials’ provenance, longevity and quality of workmanship. Finding a way to combine all these elements was one of the big challenges during the initial development.
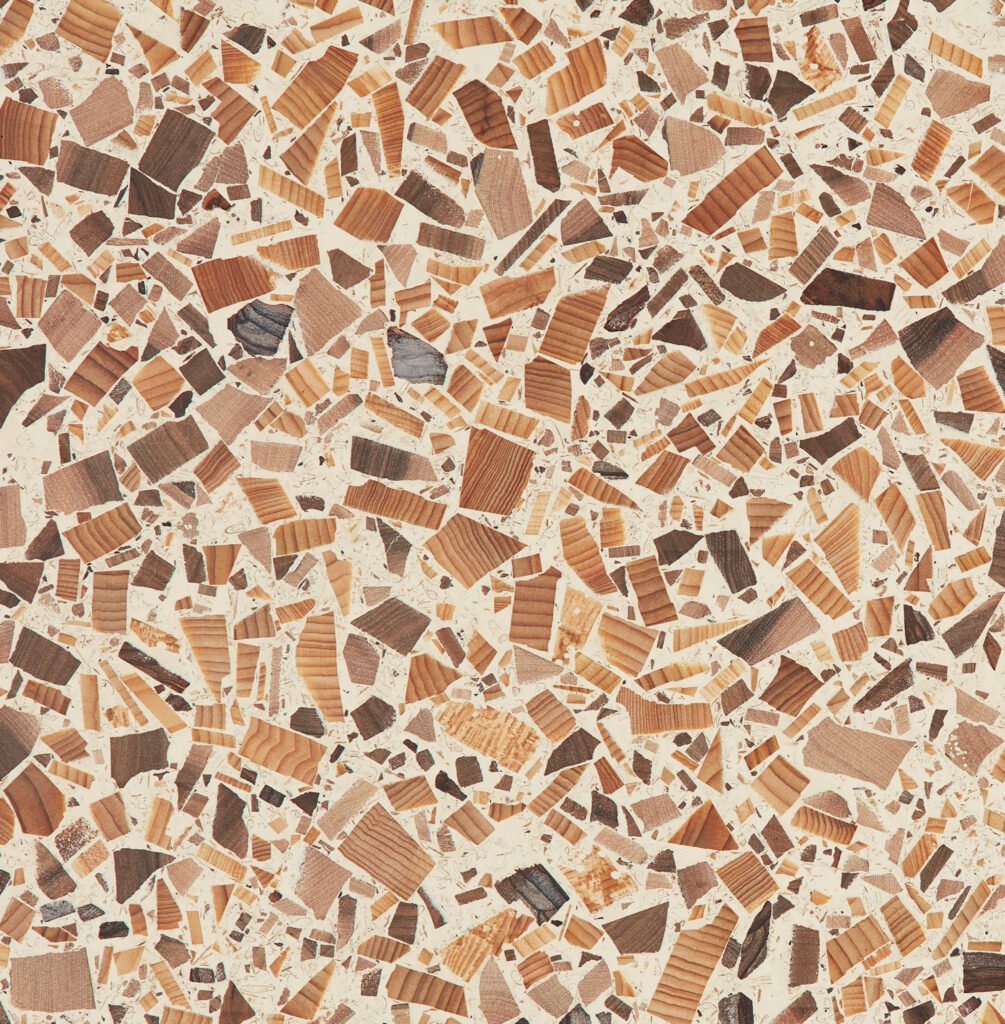
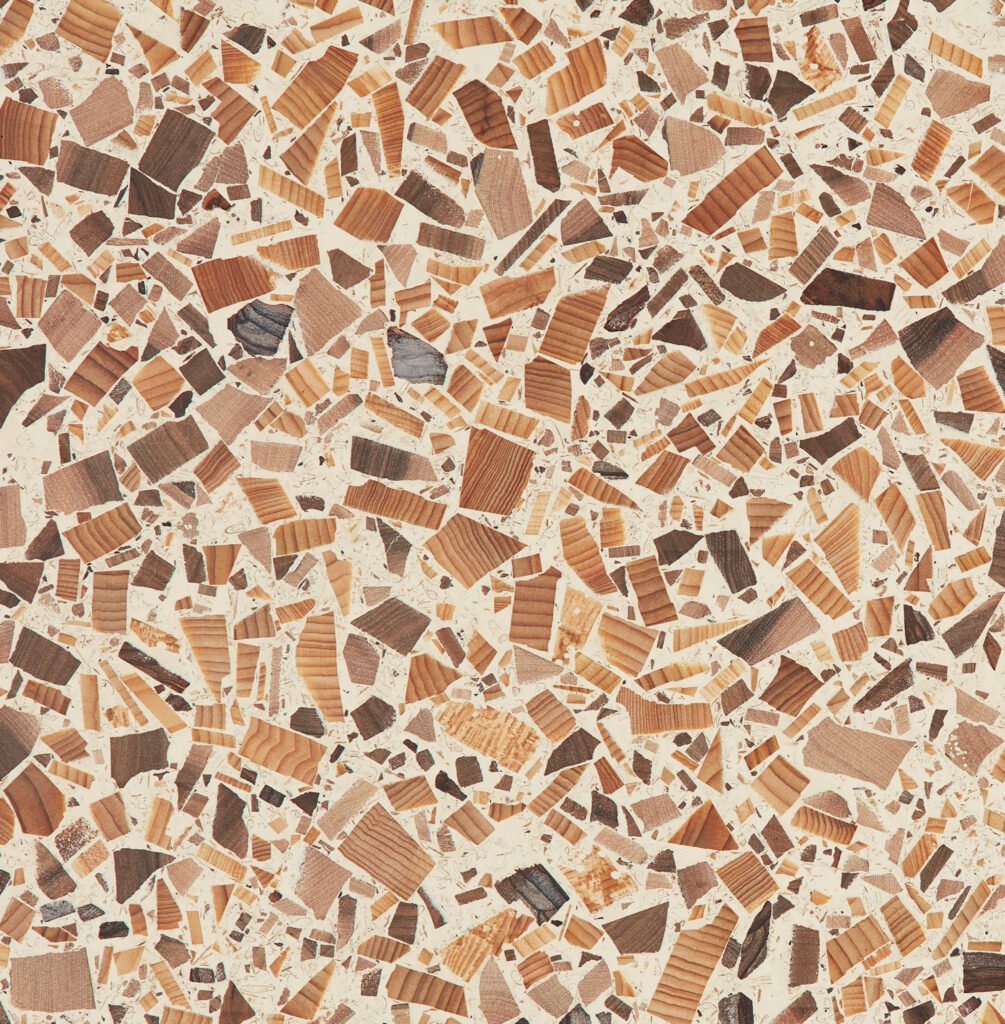
“Sustainability is not just about recycling; it’s also about knowledge of your materials’ provenance, longevity and quality of workmanship.”


How is the creation process for Foresso different from other aggregate tile materials, like stone tile terrazzo?
We’ve adapted machinery and processes from both woodworking and stone terrazzo, and although it is similar in some ways, our in-house processes involve a lot of techniques from different industries. For instance, we modified a machine that is for processing animal feed to produce our end-grain wood chips.
The major difference between the two is that most stone terrazzo is cast in huge blocks and then cut down to size, while we hand-cast each sheet individually, allowing a much greater freedom to designers to specify what they want as well giving a greater attention to detail to ensure high standards.
What would you say are perceived advantages and plusses of handmade products as compared to manufactured ones?
Each handmade object will have little differences, even if they are the same piece, and it is this individuality and connection to the person who made it that is the biggest advantage for a handmade product. Handmade also tends to imply smaller batches, which means that it is easier to make better choices about sustainability and ethical responsibility as changing the supply chains and processes of very large manufacturing industries is extremely difficult.
What are some of your inspirations when it comes to blending various materials in a tile? What informs the mix and the hues that result from such a blend??
Some of my early inspiration actually came from cooking. I’m a keen home cook and baker. The order of combining ingredients or how they are mixed informed some of my early tests, whether it was mixing wet into dry, how workable the mix was, or how to get things to bind well. The standard collection I designed was inspired by parts of London that are familiar to me and tell a story of the city. By doing this, I hoped to show people that they could use a material that could tell their story and of their project. For instance, our colorway Bianco Mono, which is London Plane timber in a white binder, was inspired by West London’s Holland Park neighborhood.
After the first tests, it was trial and error across hundreds (if not thousands) of samples to find the right consistency, how to get the binder to stick well to the timber and how to use more waste wood in the mix. Scaling up to sheet sizes was the biggest challenge, as there are always unexpected challenges when you change the scale of any kind of production. The color of the binder was the easiest part, as there is a well-established supply chain for the kind of pigments we use, allowing us to change the look of the sheets as we want.
Charcoal Mono Ivory Duo
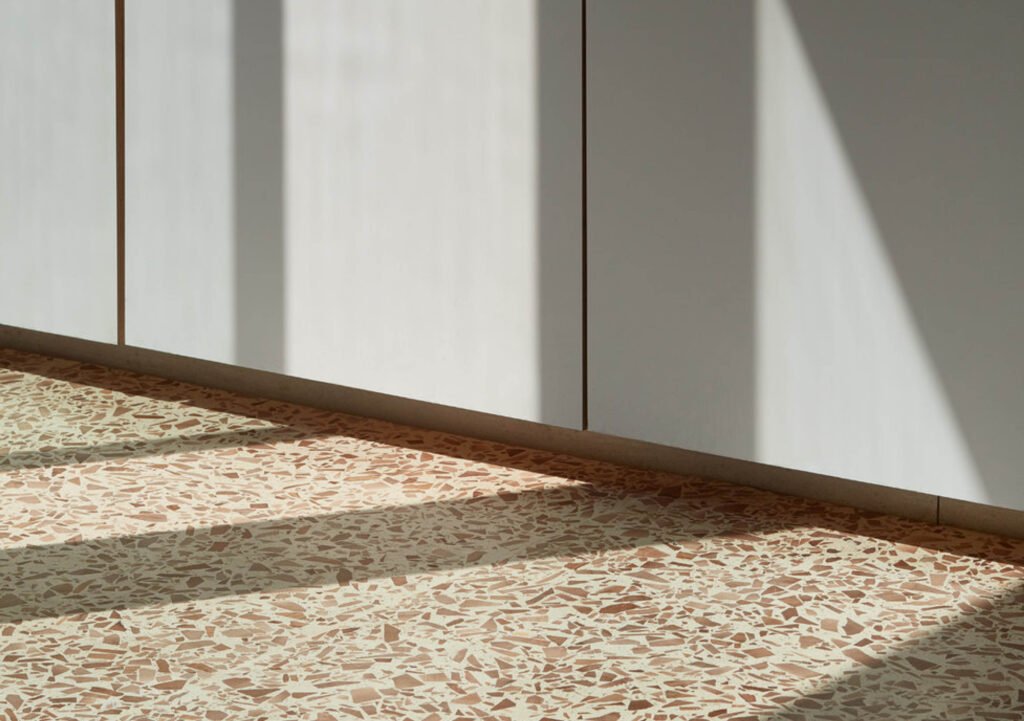
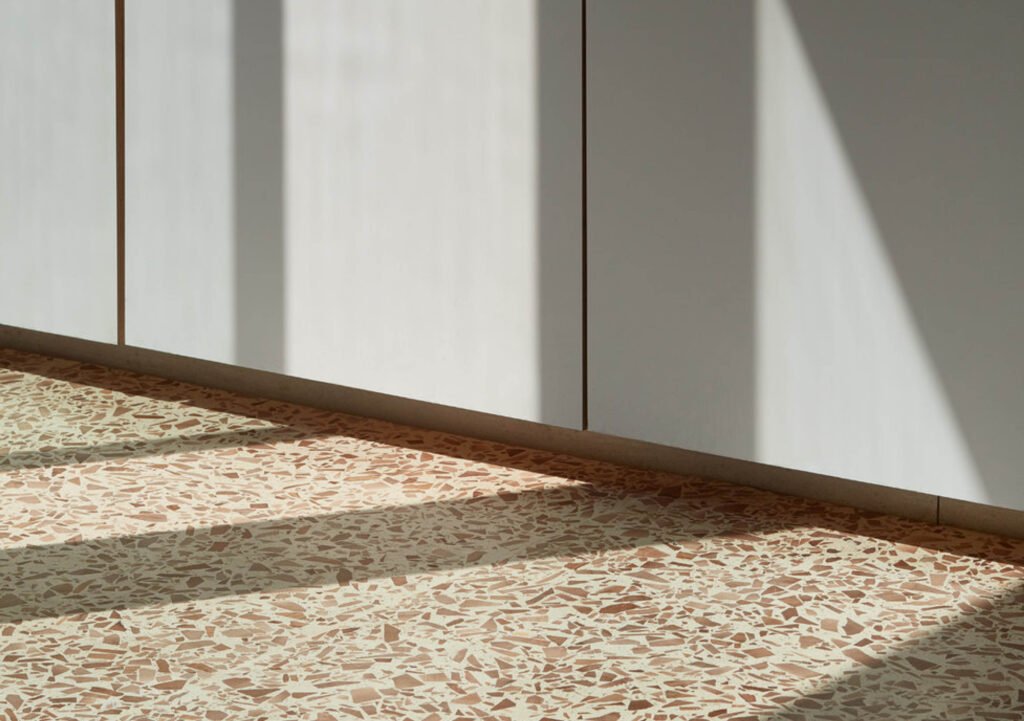
How has the market reacted to Foresso?
From the start I had a clear “brand” in mind, although really it is a reflection of how we approach manufacturing and of our thinking in general. I want to be honest about the day-to-day difficulties of trying to be a sustainable manufacturer while still offering something beautiful and adaptable that can be used to tell the story of a project. In recent years, there has been a huge shift towards sustainability in design, so the reaction to Foresso has been extremely positive.
I hope that by encouraging people to get emotionally and intellectually invested with their materials, we can help make better choices in architecture and design.
We’ve seen your suggested uses for Foresso, but were there other applications by clients that surprised you?
Miter-joined skirting that matches the Foresso floor has been one of my favorite uses; it had this brilliantly modern yet classic look about it and was a really smart way to use every last bit of the sheets.
There seems to be a growing movement towards handmade objects and artisanal products. Why do you think this is so?
I think it’s as simple as people wanting to feel a connection to others, and although computers have allowed mass manufacture to get even bigger and more homogeneous, it has also allowed the resurgence of craft and small companies who can now find their audience and survive without being tied to one tiny physical location. Handmade products are one of the few things that you can find this with, and it is nice to feel that you are also supporting a small business rather than a gigantic corporation.
Did you have any realizations or insights since creating Foresso that made a mark on you as a creative?
It’s okay to go against the accepted way of doing things and that we can stand our ground without having to bend to what people think the market wants. It’s been amazing to find an audience that responds positively to this. At the moment, I’m just loving seeing it grow, knowing how far we’ve come, and that by continuing to make better choices each day, we can achieve a lot more.


Do you allow client customization of the materials and hues used in a Foresso tile?
Adapting Foresso is something that can help tell the story of a project, whether through custom binder colors or custom timber. The only catch is that we will only source off-cuts of British timber. Some of our clients ask us to source timber from specific locations or come to us with a reference we then work to.
Where do you source your raw materials for Foresso?
We source as much of our materials locally as we can. Our timber is all from Britain, a lot of it coming from London, and the rest from within 100 miles of us. We are very strict about our materials policies and source everything as responsibly as possible, whether by choosing formaldehyde-free, FSC plywood or by working to eliminate single-use plastics within the workshop.
Your ethical stance in the creation of materials that are sustainable and environmentally-friendly is admirable. You arrived at a turning point where you and your partner Jake Solomon decided to cut production of resin panels. What prompted this business decision, and what challenges did you encounter after this move?
When I first approached Jake, I had thought Foresso was fairly ready to go, but together we have developed it significantly. The more we worked on it and talked to people about it, the more we realized the potential in sustainable manufacturing and that we could do it the way that we wanted to. Both of us had long wanted to take an ethical stance and engage with sustainability, and it felt like the time was right for it. After we announced our shift away from resin panels for ethical and ecological reasons, we had mixed reactions. Some people were overjoyed to hear that we were taking a stand, and some didn’t think that it was a good idea because they liked the resin panels. In the end, the change has had a hugely motivating effect on us and it’s been wonderful to get such a good response.
Moving and then setting up our new production facility has been a massive undertaking, but we are getting settled in now and have been building an excellent production team who are really engaging with what we are trying to do. For us, it’s been all about constantly improving and constantly trying to make better choices in everything we do
Where do you intend to take Foresso next? Any new sustainable materials in the pipeline to look forward to?
We are currently in production at our new facility and are scaling up to meet demand, but we have still have long term goals for Foresso as a material to reach our ethical goals. We are aiming to make it 100% recycled and are currently working with some exciting institutions that specialize in sustainable materials and are helping us make this a reality. •
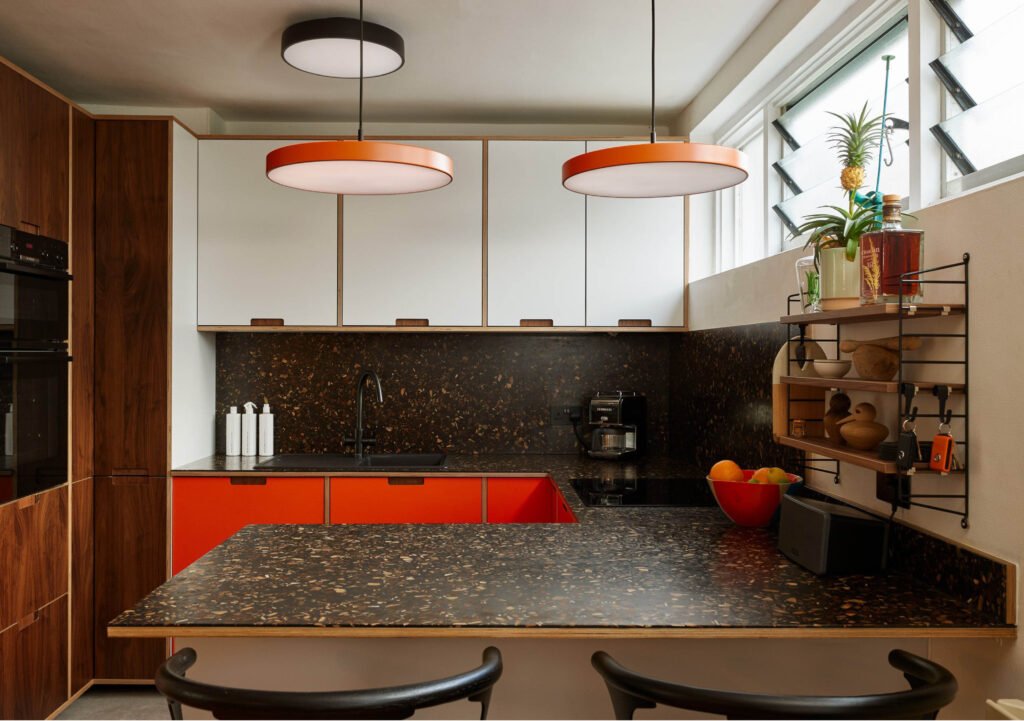
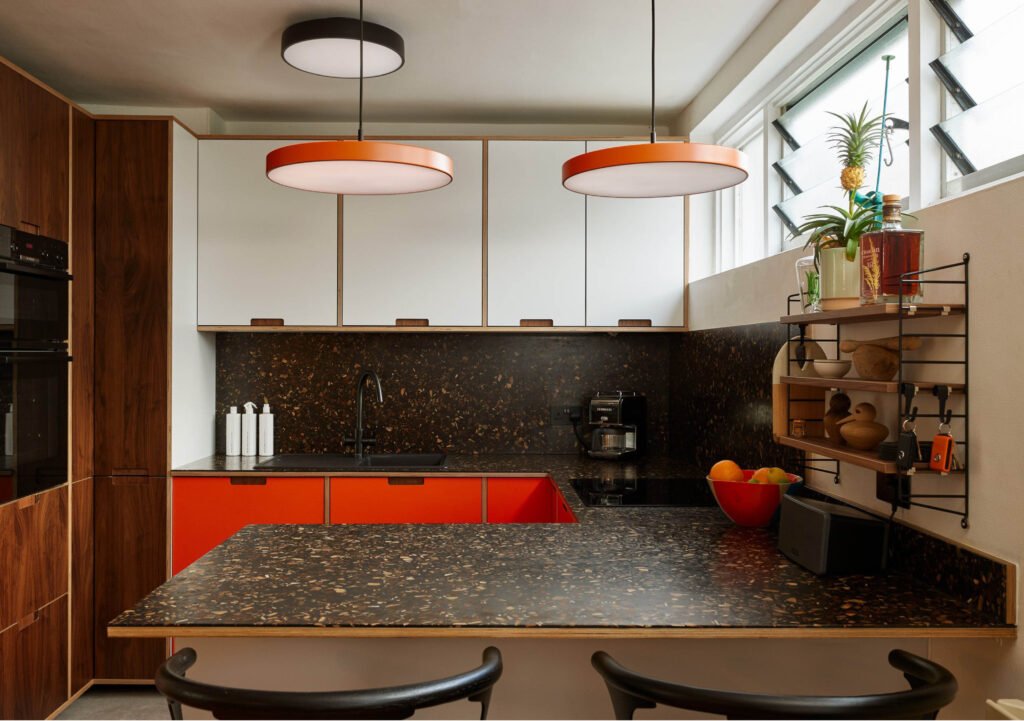
This interview first appeared on Kanto’s 2018 Craft issue.